Luftfahrt: Die neue Logik des Fliegens | ABC-Z
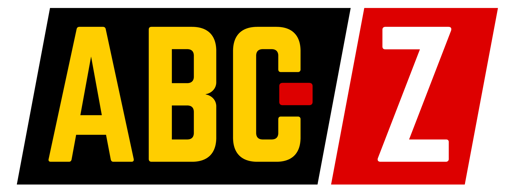
Die neue A321XLR von Airbus wird in den Liniendienst eingeführt. Die Airlines wollen mit diesem mittelgroßen Flugzeug und dessen Komfort die Langstrecke neu definieren. Auch dem Standort Hamburg bringt die Produktion der Maschine erhebliche Modernisierungen.
André Walter freut sich über Entwicklungen, die man vor einigen Jahren noch gar nicht so sehr im Blick hatte. Der Chef des zivilen Flugzeugbaus von Airbus in Deutschland steht in der hochmodern ausgestatteten Produktionshalle 246 auf dem Gelände der Flugzeugwerft in Hamburg-Finkenwerder. „Die Logistik wird heutzutage deutlich höher gewichtet als früher“, sagt der Manager, der seit 18 Jahren für Airbus arbeitet. Seinerzeit galten Logistikflächen eher als Kostenfaktor. Mittlerweile ist eine exakt steuerbare Anlieferung von Teilen für die immer dichter getaktete Produktion von Flugzeugen eine unverzichtbare Voraussetzung.
In der Halle 246 wurden früher Kabinen in den Riesenjet A380 eingebaut, doch dessen Produktion endete im Jahr 2021. Heutzutage läuft in der Halle die sogenannte Strukturmontage, die Fertigung von Rumpfsegmenten, für das neue Langstreckenflugzeug A321XLR. Die Maschine zählt zur „A320-Familie“ von Airbus, einem Sortiment von Kurz- und Mittelstreckenflugzeugen mit jeweils einem Mittelgang. Mithilfe eines zentralen Zusatztanks, der hier in der Halle in den Rumpf eingebaut wird, und mit einem weiteren, flexiblen Tank im Laderaum, kann die A321XLR bis zu 8700 Kilometer weit fliegen – sie ist ein relativ kleines Flugzeug mit einer großen Reichweite, die den Fluggesellschaften zusätzliche Flexibilität in ihrer Routenplanung verschaffen wird. „Es gibt derzeit kein der A321XLR vergleichbares Flugzeug am Markt“, sagt Walter. „Die A321XLR erweitert das Angebot und zielt auf einen spezifischen Marktbedarf ab.“ Die spanische Fluggesellschaft Iberia führt das Flugzeug voraussichtlich im November als erste Airline ein.
Die A320-Maschinen und ihre Varianten sind die weitaus wichtigste Produktreihe für Airbus, den vor Boeing weltweit führenden Hersteller von Zivilflugzeugen. Mehr als 7000 Bestellungen für die „A320-Familie“ hat Airbus in den Orderbüchern. Die A321LR („Long Range“), die 2018 erstmals abhob, hat bereits eine erhöhte Reichweite von 7400 Kilometern. Doch offenbar geht noch mehr. Allein 500 A321XLR („Extra Long Range“) wurden seit der Präsentation des neuen Modells im Jahr 2019 von insgesamt 25 Fluggesellschaften bestellt. „Die A321XLR sieht auf den ersten Blick aus wie ein ganz normales Mitglied A320-Familie, sie ist wegen ihres speziellen Profils aber ein absoluter Spezialist“, sagt der Hamburger Luftfahrtexperte Cord Schellenberg. „Deshalb zähle ich diesen neuen Airbus, anders als seine Geschwister, zum Langstreckenangebot von Airbus. In diesem Segment mit höheren Entwicklungs- und Produktionskosten ist ein Auftragsbestand von mehr als 500 Jets noch vor der Auslieferung des ersten Serienflugzeugs ein sehr guter Wert.“
Hamburg-Finkenwerder ist nach den Konzernzentralen von Airbus in Toulouse und Boeing in Seattle der weltweit drittgrößte Standort für den Bau von Zivilflugzeugen – und der weitaus wichtigste Standort für die Fertigung der A320-Familie. Airbus modernisiert die Produktion an der Elbe kontinuierlich. Die Neueinführung der A321XLR hat der Flugzeugwerft allerdings einen ungewöhnlich starken Schub in kurzer Zeit gebracht. „Wir haben für das Flugzeug eine Halle – zur Ausrüstung von Rumpfsegmenten – komplett neu gebaut, eine frühere Halle aus dem A380-Programm für die Strukturmontage der A321XLR umgebaut und eine Halle für die Pilotlinie der Endmontage der A321XLR teilweise umgewidmet“, sagt Walter.
Modernisiert wird die Logistik zur Anlieferung der Teile an die jeweiligen Stationen. Vorangetrieben wird auch die Automatisierung einzelner Arbeitsschritte – und generell die Digitalisierung. In die Halle 246 kommen die Rumpfschalen aus Aluminium von Lkw über einen Schwerlastaufzug. An einem Schienensystem laufen sie unter der Decke einer Zwischenebene entlang, der „Mezzaninebene“. Von einem Kran werden die Teile mithilfe von Lasern und Sensoren automatisch in die optimale Position auf einer mobilen Produktionsbühne gebracht. „Mit dieser Zwischenebene können wir auch die Höhe der Halle optimal nutzen“, sagt Kai Spille, Projektleiter für die Entwicklung, den Ausbau und die Inbetriebnahme der neuen Strukturmontage-Linie in Halle 246. „Die Produktionstechnik hier ist die neueste, die am Markt zur Verfügung steht.“
Flugzeugbau ist immer noch und auch weiterhin Manufakturarbeit. Airbus versucht dennoch, so viel wie möglich davon zu automatisieren – für eine höhere Effizienz, und um die Belastung etwa jener Männer und Frauen zu senken, die in den gewölbten Rümpfen in anstrengender Körperhaltung Teile und Material montieren. „Die Ergonomie hat heutzutage einen hohen Stellenwert“, sagt Walter. „Sie ist, mit Blick auf die Gesundheit der Mitarbeitenden, ein zentraler Faktor.“ Vieles versucht der Flugzeugkonzern dabei aus anderen Branchen zu lernen. Doch deren Technologien lassen sich nur begrenzt übertragen. „Wir brauchen sehr stark spezialisierte und angepasste Robotik für die Montage von Flugzeugrümpfen“, sagt Walter. „Standardlösungen zum Beispiel aus der Automobilbranche helfen uns hierbei nicht weiter. Wir entwickeln Systeme zur Automatisierung teils auch bei Airbus selbst.“ Maschinen zum Beispiel für das Nieten oder Schrauben von Verbindungen.
Die Halle 259, in der die Rumpfsegmente für die A321XLR ausgestattet werden, hat Airbus komplett neu gebaut. Sie gilt als eine der modernsten Produktionsstätten im international weitverzweigten Baukastensystem des Konzerns. „Wir liefern das Material für die Ausrüstungsmontage hier automatisiert direkt an die Rumpfsegmente, das ist eine der wesentlichen Innovationen in der Logistik unserer Produktion“, sagt Gunnar Brinkmann, stellvertretender Produktionsleiter der Ausrüstungsmontage A321XLR. „Bei Airbus ist das aktuell noch einzigartig. Wir können Störungen antizipieren, das beschleunigt die Durchläufe.“ Digital sind mittlerweile auch immer mehr Werkzeuge am Band – die Baupläne für die einzelnen Arbeitsschritte lesen die Mitarbeitenden heutzutage von Tablets ab und nicht mehr vom Papier. Und auch der alte Druckluftschrauber ist passé. „Wir nutzen stattdessen smarte Akkuschrauber“, sagt Brinkmann. „Damit können wir genaue Informationen über die Qualität der Schraubverbindung dokumentieren und Fehler vermeiden.“
Gut ist in der Ausrüstungsmontage zu sehen, wie der Zentraltank in den Rumpf der A321XLR integriert wird, der sogenannte „Rear Center Tank“, der 13.000 Liter Kerosin fasst und der die Tanks in den Tragflächen ergänzt. Um für den Tank Platz im Rumpf zu sparen, liegen etliche Leitungen und Installationen offen in den Schächten des Hauptfahrwerks. Dieses und andere Konstruktionsmerkmale unterscheiden das Langstreckenflugzeug erheblich von allen anderen Mustern der A320-Familie. Der etwas größere Kasten des Fahrwerks ist allerdings die einzige auffällige Veränderung, durch die man eine A321XLR von außen auf den ersten Blick erkennen kann.
Airbus schafft mit der A321XLR einen Markt, den es bislang in dieser Form nicht gab. Mit dem doppelstöckigen Riesenjet A380 wollte der Konzern in den Nullerjahren das Konzept der Knotenpunkte unterstützen – mehr als 500 Menschen je Maschine fliegen mit der A380 von einem Großflughafen zum nächsten, und von dort aus gelangen sie mit einem kleineren Flugzeug zum Ziel. Doch die Strategie ging nicht auf, die Produktion der A380 wurde nach wenigen Jahren wieder eingestellt.
Nun kommt etwas Neues in Gang. „Immer mehr Passagiere wünschen sich Langstreckenflüge abseits der Mega-Strecken wie London–New York oder Frankfurt–Bangkok mit entsprechend zeitaufwändigen Zu- und Abbringerflügen aus den Regionen“, sagt Luftfahrtexperte Cord Schellenberg. „Sie wollen nonstop von Hamburg nach New York oder von Venedig nach Bangkok fliegen, um Zeit zu sparen. Und das bei gleich hohem Bordkomfort wie in den Großraumflugzeugen, insbesondere in der Business Class.“ Mit der A321XLR spreche Airbus gezielt jene Fluglinien an, „die über Strecken mit weniger Passagieraufkommen, aber hohem Ertragspotential in Bezug auf Geschäftsreisende verfügen. Mit dem neuen Flugzeug können die Airlines Nonstop-Verbindungen anbieten, die mit einem 300-Sitzer nicht wirtschaftlich zu fliegen sind.“
Bei der Innenausstattung in der XLR-Version will Airbus den Komfort der Langstrecke – von Großraumflugzeugen wie der A350 mit zwei Kabinengängen – auf ein kleineres Flugzeug mit einem Mittelgang übertragen. Anders würde sich für bis zu elfstündige Flüge mit der neuen Maschine wohl kein dauerhaftes Publikum finden lassen. Im Airspace Customer Definition Centre, einem eigenen Gebäude auf der Flugzeugwerft, erklärt Ingo Wuggetzer, wie das funktioniert: mit neuartigen Sitzen, schmaleren Kabinenwänden, aufwändigem Deckendesign. „Wir haben die Marke ,Airspace’ 2016 für die A350 eingeführt und haben das Konzept bereits auf die A321LR als Option übertragen“, sagt Wuggetzer, Leiter Kabinenmarketing bei Airbus. „Für die A321XLR wird die Airspace-Kabine als Standard eingeführt.“
Ein entscheidendes Element für den Langstreckenflug ist die Beleuchtung der Kabine. „Bei den Airspace-Beleuchtungsszenarien können wir mit insgesamt 16,7 Millionen Farbvarianten arbeiten“, sagt Wuggetzer. „Das Licht ist enorm wichtig auf den Langstrecken, für die Kabine insgesamt, für das Raumgefühl wie auch für die Sanitärräume und die Ausleuchtung der Mahlzeiten. Der Jetlag lässt sich damit um drei bis vier Stunden reduzieren.“ Bis zu 244 Passagiere passen in eine A321XLR. Im Durchschnitt der bisher bestellten Maschinen werden 160 Sitze für drei bis vier Klassen montiert, sagt Wuggetzer.
Mehr Raum für die Sitze in der A321XLR gewinnt Airbus vor allem auch durch deren Bauweise – und spart damit zugleich Gewicht und Treibstoff ein: „Unser leichtester Sitz in der Economy wiegt heutzutage etwa sieben Kilogramm, noch vor wenigen Jahren waren es mehr als zwölf Kilogramm“, sagt Wuggetzer. „Die Bauweise wird immer stabiler und zugleich leichter bei gleichbleibendem Komfort. Das erreichen wir unter anderem durch Hightech-Stoffsegel anstelle von dicken Schaumstoffpolsterungen in der Rückenlehne.“
Die Gepäckfächer für die A321XLR wiederum sehen im Ausstellungsraum so aus wie diejenigen vieler anderer Flugzeuge auch. Doch die neuen Fächer sollen den Passagieren und den Besatzungen das Boarding und das Verlassen des Flugzeugs künftig wesentlich erleichtern – nicht nur auf Langstrecken. „Unsere neu designten Gepäckfächer in der Airspace-Ausstattung können 60 Prozent mehr Gepäckstücke aufnehmen, die jeweils 40 Prozent größer sein können als bislang“, sagt Wuggetzer. „Vor allem erreichen wir das dadurch, dass man das Handgepäck stehend im Gepäckfach verstauen kann.“
Nach dem Fabrikrundgang sitzt André Walter in seinem Büro in einem der vielen Gebäude auf der riesigen Flugzeugwerft. Die A321XLR für die Markteinführung bei Iberia ist fertig gebaut, die Produktion des neuen Flugzeugs läuft hoch. Bis zum kommerziellen Erstflug war es ein schwieriger Weg. Entwickelt und vorangetrieben wurde die A321XLR mitten in der Pandemie. „Die größte Veränderung war für uns hier in Hamburg, dass die A321XLR weitgehend digital und virtuell – großteils während der Pandemie – eng vernetzt über alle im Airbus-Konzern beteiligten Standorte hinweg entwickelt worden ist“, sagt der Manager.
Konzernweit fuhr Airbus 2020 die Produktion herunter – und seit 2022 wieder herauf. Bis zum Jahr 2027 soll die Produktion der gesamten A320-Familie auf monatlich 75 Maschinen steigen, von heutzutage vermutlich rund 60 Stück, die genaue Zahl nennt Airbus nicht. 18.000 Airbus-Mitarbeiter arbeiten derzeit auf Finkenwerder, zudem 2000 Leiharbeitskräfte. Allein 1000 neue feste Mitarbeiter hat Airbus in Hamburg seit 2022 eingestellt – nachdem zuvor allerdings etliche Stellen gestrichen worden waren. Zum Hochlauf der Produktion soll die A321XLR einen wesentlichen Beitrag leisten.
Obendrein hat das Flugzeug für Airbus aber noch eine ganz andere Funktion. Die A321XLR schafft eine Brücke hin in eine Zukunft, in der Flugzeuge ohne Ausstoß von Treibhausgasen fliegen sollen, etwa mit regenerativ erzeugtem Wasserstoff. Um Wasserstoff an Bord speichern zu können, werden alle Jets der kommenden Jahrzehnte als Standardbauteil vermutlich zentrale Tanks im Rumpf benötigen. „Mit dem Einbau des Rear Center Tanks in die A321XLR lernen wir sehr viel für künftige Rumpfarchitekturen“, sagt Walter, „die wir womöglich auch für mit Wasserstoff betriebene Flugzeuge brauchen werden.“
Olaf Preuß ist Wirtschaftsreporter der WELT AM SONNTAG für Hamburg und Norddeutschland. Zu seinen Schwerpunktthemen zählen die Weiterentwicklung und der Bau von Flugzeugen, über die er seit mehr als 25 Jahren berichtet, vor allem über Airbus und das Netzwerk der Luftfahrtbranche in der Metropolregion Hamburg.