Eagle Burgmann in Eurasburg: Roboter an den Regalen – Bad Tölz-Wolfratshausen | ABC-Z
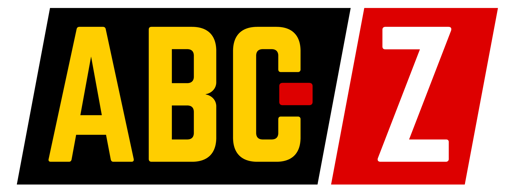
Ins Herz des automatisierten Lagers im Eurasburger Werk von Eagle Burgmann kann man durch eine große Glasfront blicken. Von drinnen aber hört man nichts. Scheinbar lautlos fahren die 24 jeweils knapp einen Meter langen und kaum mehr als einen halben Meter hohen, akkubetriebenen Roboter auf dem Gerüst mit den darunter eingepassten Behälterboxen. Auf 48 mal 28 Metern Fläche stapeln sich jeweils acht der grauen Kisten übereinander. Darin liegen die verschiedenen Komponenten für die Gleitringdichtungen, die das Unternehmen im zentralen Eurasburger Leitwerk für die globale Produktion fertigstellt. Wie die Roboter über die Boxen gleiten und die verschiedenen, zur späteren Montage benötigten Teile auswählen, wirkt wie eine perfekt einstudierte Choreografie.
Den Beschäftigten spart das vor allem viel Zeit. Vom „schnellsten Lagersystem der Welt pro Quadratmeter“ spricht Martin Pitsch, Vice President Operations bei Eagle Burgmann, und meint damit, dass es bis zu viermal mehr Kapazität auf gleicher Fläche biete als das bisherige Lagersystem. Zudem sparten sich die Mitarbeiter Laufwege, waren sie doch bisher nach Unternehmensangaben bis zu 15 Kilometer täglich unterwegs, um die benötigten Teile zusammenstellen.
Damit ist zugleich auch ein zentrales Strategieziel von Eagle Burgmann beschrieben: schneller zu werden. „Wir wollen die Auswahl der optimalen Dichtungslösung für unsere Kunden von Tagen auf Stunden, die Dichtungsproduktion von Monaten auf Wochen reduzieren“, erklärt Martin Pitsch. „Das übergeordnete Ziel ist, die Kunden schneller zu beliefern“, sagt der promovierte Ingenieur, der seit drei Jahren für das globale Produktionsnetzwerk von Eagle Burgmann zuständig ist. „Dafür reduzieren wir die Komplexität bei Produkten und Prozessen.“
Die Produkte des Unternehmens sind überall dort gefragt, wo es darum geht, flüssige oder gasförmige Medien zu transportieren, also etwa Kompressoren, Rührwerke oder Pumpen zuverlässig abzudichten. Daher sind die Komponenten in so vielen unterschiedlichen Branchen zu finden, in Anlagen und Pipelines der Öl- und Gasbranche, der Lebensmittel- und Getränkesparte, der Pharmazie und Chemie oder auch dem Bergbau und der Schiffstechnik. Gemeinsam haben all diese Anwendungen, dass ihre Funktion durch den Einsatz der Dichtungen aus Eurasburg verlässlicher und nachhaltiger wird. In Meerwasserentsalzungsanlagen werden die Dichtungen genauso verwendet wie dazu, Kohlenstoffdioxid unter Wasser sicher einzulagern, aktuell etwa in der Nordsee vor dem niederländischen Rotterdam.
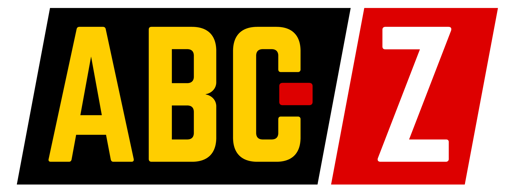
Das Angebot an Dichtungen bei Eagle Burgmann ist daher so mannigfaltig wie komplex und reicht von Massenprodukten wie Gummibalg-Dichtungen bis zu Hightech-Lösungen in geringen Stückzahlen für Kompressoren oder Rührwerke. Mehr als 200 000 Artikel habe man aktiv im Angebot, sagt Pitsch. Die Produkte enthielten zwischen acht und 50 Bestandteile, ihre Preise variierten zwischen zehn und 200 000 Euro.
Damit die Monteure später genau die richtigen Teile für die komplexeren Dichtungen bekommen, visualisieren Bildschirme an den Arbeitsstationen die zu verarbeitenden Produkte. Dieser zusätzliche Sicherheitsfaktor soll ausschließen, dass etwas verwechselt wird. Als einer der Behälter auf dem Förderband vor einer Mitarbeiterin stoppt, leuchtet ein Laser auf die Teile, die gerade gebraucht werden. Die Behälter können für verschiedene Komponenten mehrfach unterteilt sein. Obendrein zeigt der Bildschirm an, welche Anzahl benötigt wird.
Wenn Monteure aus diesen Teilen später von Hand die hochkomplexen Dichtungen zusammensetzen, kann das von einigen Stunden bis zu mehreren Tagen dauern. So präzise müssen die Spezialisten arbeiten. Schließlich müssen die Spezialdichtungen teils hohen Druck bis zu 450 bar und zehntausende Umdrehungen aushalten. Daher testet Eagle Burgmann die Produkte zur Qualitätskontrolle auf Prüfständen.
Auf 40 000 Quadratmetern Fläche sind in Eurasburg 700 Mitarbeiter tätig
Das Eurasburger Werk mit einer Fläche von 40 000 Quadratmetern und 700 Mitarbeitern ist das wichtigste und größte des gesamten Unternehmens – und soll deshalb als Leitwerk für alle restlichen Produktionsstandorte des Dichtungsherstellers gelten, der zu den Weltmarktführern gehört. Automatisierungs- und Digitalisierungsprozesse spielen dabei eine wichtige Rolle. Dafür investiert Eagle Burgmann in Eurasburg seit 2021 zweistellige Millionensummen, weitere Investitionen werden für die Initiative „Eurasburg 2027“ in den kommenden drei Jahren noch hinzukommen.
Das automatisierte und digitalisierte Lagersystem aufzubauen, hat allein 4,8 Millionen Euro gekostet und ein knappes Jahr gedauert – von Juli 2023 bis Anfang Mai dieses Jahres. Schon 2022 hatte Eagle Burgmann begonnen, in Eurasburg grundlegend umzubauen. „In zehn Monaten haben wir 115 Maschinen umgezogen“, berichtet Pitsch. Einige laufen inzwischen vollautomatisch. In dem hochmodernen Maschinenpark können die Beschäftigten den Herstellungsprozess über Bildschirme verfolgen, Produktionsdaten überwachen und eingreifen, falls Parameter vom Sollzustand abweichen.
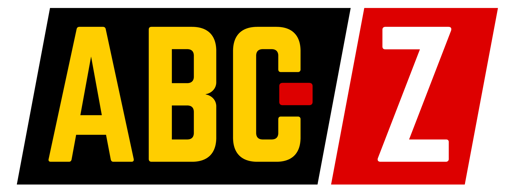
Das alles gehört zum umfassenden Transformationsprozesses in dem Unternehmen, das ein Joint Venture der deutschen Freudenberg Gruppe und der japanischen EKK Group ist. So errichtet Eagle Burgmann derzeit an seinem Hauptsitz in der Nachbarkommune Wolfratshausen für 20 Millionen Euro noch ein neues „Innovation Center“ für Forschung und Entwicklung.
Alle Standorte von Eagle Burgmann verbindet das Produktionssystem „Glad“. Das englische Wort für froh steht bei dem Unternehmen auch als Abkürzung für die vier Begriffe Green, Lean, Automated und Digital – also grün, schlank, automatisiert und digital. Dieses System beginnt laut Pitsch mit nachhaltiger Produktionsweise, etwa indem das Unternehmen kontinuierlich seinen Ressourceneinsatz optimiert. Es setzt sich mit schlanken Prozessen fort, bei denen die Variantenvielfalt bei Dichtungen reduziert werden soll, um mehr vielfältig anwendbare Baukastenlösungen anzubieten. Automatisierung und Digitalisierung bedeutet auch, Prozesse transparent zu gestalten, sodass Mitarbeiter über zentrale Bildschirme auf alle wichtigen Kennzahlen im Eurasburger Werk zugreifen können – im Sinne einer prozessorientierten Vernetzung. Arbeitssicherheit und das Wohlergehen der Beschäftigten stehen in Eurasburg gleichwohl im Fokus. Um die Brandgefahr zu minimieren, herrschen in dem automatisierten Lagersystem Sauerstoffbedingungen wie auf 4000 Höhenmetern.
Und natürlich geht es auch um die Einsparung von Arbeitskräften. Zu automatisieren und zu digitalisieren sei auch wichtig, um gegen den Fachkräftemangel, den auch Eagle Burgmann spüre, gewappnet zu sein, erklärt Pitsch. Definitiv seien aber umso mehr spezialisierte ausgebildete Mitarbeiterinnen und Mitarbeiter vonnöten, für die es jedes Jahr zwölf Ausbildungsplätze gebe. Die Ausbildung gestalte Eagle Burgmann möglichst vielfältig und biete jungen Menschen internationalen Austausch und Arbeitseinsätze im Ausland an. Dass der Dichtungshersteller mit seiner Produktion in der Kommune bleibt, steht durch die vielfältigen Innovationen im Werk praktisch außer Zweifel. „Es gibt kein stärkeres Bekenntnis zum Standort Eurasburg als eine solche Serie von Investitionen“, hebt Pitsch hervor.